Piston
Cost Estimation for this product is under upgradation. For any query or support please email us at 'info@estisource.com'.
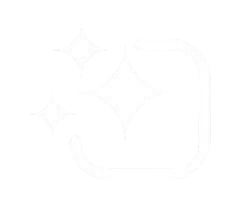
One Click Product Costing
Processing your request...

Piston
is a crucial component in many mechanical systems, particularly in internal combustion engines, hydraulic systems, and pneumatic systems. It is a cylindrical part that moves back and forth within a cylinder, creating mechanical energy through its reciprocating motion.Pistons
are fundamental to the operation of many mechanical systems, providing essential functions in engines, hydraulic and pneumatic systems, and compressors. Their ability to convert various forms of energy into mechanical work makes them indispensable in both industrial and automotive applications.1. Material Composition
▶Pistons are made from materials that can withstand high temperatures, pressures, and mechanical stresses. The choice of material depends on the application, performance requirements, and cost considerations. Here are the most common materials used for pistons:
Types of Material used for Piston:
- Aluminum Alloys
- Cast Iron
- Steel
- Composite Materials
- Considerations for Material Selection
Characterisitcs of Material:
Aluminum Alloys
Characteristics:
Lightweight: Reduces the overall weight of the engine, improving efficiency and performance.
Good Thermal Conductivity: Helps in dissipating heat quickly, reducing the risk of overheating.
High Strength-to-Weight Ratio: Offers sufficient strength while keeping the piston lightweight.
Common Alloys:
4032 Aluminum: Contains silicon for improved wear resistance and reduced thermal expansion.
2618 Aluminum: Known for higher strength and resistance to thermal fatigue, often used in high-performance engines.
Applications:
Widely used in automotive and motorcycle engines.
Preferred in racing engines for their high performance.
Cast Iron
Characteristics:
Durable and Strong: Provides excellent wear resistance and can handle high loads.
Good Damping Properties: Reduces vibration and noise, contributing to engine smoothness.
Applications:
Often used in heavy-duty diesel engines.
Suitable for applications where longevity and robustness are critical.
Steel
Characteristics:
Extremely Strong: Can endure high stresses and temperatures without deforming..
Resistant to Wear and Fatigue: Offers superior durability compared to other materials
Applications:
Used in high-performance and high-stress applications, such as in motorsport and high-performance diesel engines.
Ideal for pistons in large industrial engines.
Composite Materials
Characteristics:
Advanced Performance: Custom-engineered materials can provide an excellent balance of strength, weight, and thermal properties.
Cost and Complexity: Generally more expensive and complex to manufacture compared to traditional materials.
Applications:
Emerging use in high-tech and specialized engines, where performance requirements justify the higher cost.
Considerations for Material Selection
Operating Conditions:
Temperature: The material must withstand the operating temperatures of the engine without degrading.
Pressure: Must handle the pressures from combustion or hydraulic/pneumatic operation.
Performance Requirements:
Strength: Needs to resist mechanical stresses and impact loads.
Thermal Conductivity: Efficient heat dissipation to avoid overheating.
Weight: Lighter materials contribute to better performance and fuel efficiency.
Manufacturing and Cost:
Ease of Machining: Some materials are easier to machine into precise shapes and dimensions.
Cost: Budget constraints often play a role in material choice.
2. Manufacturing Process
▶Pistons are manufactured using various processes, each tailored to meet specific performance requirements and production volumes. Here are the primary methods of piston manufacturing along with details of the processes:
1. Casting
Process:
Mold Preparation: A mold is created in the shape of the piston. Molds can be made from sand or metal.
Melting: The piston material (usually aluminum alloy) is melted in a furnace.
Pouring: The molten material is poured into the mold.
Cooling: The material is allowed to cool and solidify in the mold.
Extraction: The solidified piston is removed from the mold.
Finishing: The piston undergoes machining processes to achieve the final dimensions and surface finish.
Advantages | Cost-Effective: Suitable for high-volume production. Versatile: Can produce complex shapes and designs. |
---|
2. Forging
Process:
Heating: A billet of piston material (commonly aluminum alloy) is heated to a high temperature.
Forming: The heated billet is placed in a forging die and mechanically pressed into the shape of a piston.
Cooling: The formed piston is allowed to cool.
Machining: The piston undergoes precision machining to achieve final specifications.
Advantages | High Strength: Produces pistons with superior strength and durability. Better Grain Structure: The forging process aligns the grain structure, enhancing the mechanical properties. |
---|
3. Powder Metallurgy
Process:
Powder Preparation: Metal powders (typically aluminum) are prepared.
Mixing: Powders may be mixed with lubricants or binders to aid in processing.
Compaction: The powder mixture is compacted in a mold under high pressure to form a green compact.
Sintering: The compacted part is heated in a controlled atmosphere to bond the powder particles without melting the whole material.
Finishing: Sintered pistons are machined to final dimensions and specifications.
Advantages | Material Efficiency: Minimal material waste compared to other methods. Complex Shapes: Capable of producing complex and precise shapes. |
---|
4. Extrusion
Process:
Billet Preparation: A billet of the piston material (usually aluminum) is prepared.
Heating: The billet is heated to a suitable temperature for extrusion.
Extrusion: The heated billet is forced through a die to create a long rod of the piston material.
Cutting: The extruded rod is cut into appropriate lengths.
Forging/Machining: The cut pieces are further processed by forging or machining to achieve the final piston shape.
Advantages | Efficient Material Use: High material utilization with minimal waste. Consistency: Produces uniform material properties throughout the piston. |
---|
3. Challenges and Limitations of Piston manufacturing
▶Manufacturing pistons involves overcoming various technical challenges and limitations to ensure high performance, durability, and efficiency. Here are some of the key challenges and limitations faced in piston manufacturing
1. Material Selection and Properties
Challenges:
High Temperatures: Pistons must withstand extreme temperatures without degrading.
Mechanical Stresses: Pistons endure high mechanical stresses during operation, requiring materials with high strength and fatigue resistance.
Thermal Expansion: Managing thermal expansion to avoid issues with clearances and fit within the cylinder.
Limitations:
Material Costs: High-performance materials like certain aluminum alloys or composites can be expensive.
Trade-offs: Balancing properties such as strength, weight, and thermal conductivity often requires trade-offs.
2. Manufacturing Processes
Challenges:
Complex Geometries: Creating complex piston geometries with intricate features can be difficult.
Precision and Tolerances: Achieving the necessary precision and tight tolerances to ensure proper fit and function.
Surface Finish: Ensuring a smooth surface finish to reduce friction and wear.
Limitations:
Process Limitations: Each manufacturing process (casting, forging, etc.) has its own limitations regarding the achievable geometries and tolerances.
Production Speed: High precision often requires slower, more meticulous production processes, affecting throughput.
3. Quality Control and Consistency
Challenges:
Defects: Detecting and minimizing defects such as porosity, cracks, and inclusions that can compromise piston performance.
Consistency: Ensuring consistent quality across large production runs.
Limitations:
Inspection Costs: High-quality control standards can increase inspection and testing costs.
Rejection Rates: Maintaining low rejection rates while producing pistons that meet stringent quality requirements.
4. Thermal Management
Challenges
Heat Dissipation: Ensuring pistons dissipate heat effectively to avoid thermal fatigue and failure.
Cooling Mechanisms: Integrating cooling mechanisms, such as oil galleries, without compromising piston integrity.
Limitations:
Design Constraints: Incorporating cooling features can complicate the design and manufacturing process.
Material Constraints: Limited material choices that combine good thermal conductivity with mechanical strength.
5. Wear and Lubrication
Challenges:
Friction and Wear: Managing friction and wear between the piston and cylinder wall to prolong engine life.
Lubrication: Ensuring adequate lubrication to prevent piston seizure and excessive wear.
Limitations:
Material Choices: Some materials may have excellent mechanical properties but poor wear resistance.
Cost of Coatings: Advanced coatings to reduce wear can add to the manufacturing cost.
4. Costing
▶Creating cost-effective pistons involves optimizing the manufacturing process to balance quality, performance, and cost. Here are some strategies and insights into the cost-effective manufacturing of pistons:
1. Casting
Advantages:
Lower Material Costs: Casting can use less expensive materials and alloys.
High Volume Production: Economical for large-scale production due to lower per-unit costs.
Flexibility: Capable of producing complex shapes in a single step, reducing the need for additional machining.
Process:
Sand Casting: Uses sand molds which are inexpensive and suitable for small to medium production runs.
Die Casting: Involves metal molds, providing better precision and surface finish, suitable for high-volume production.
Cost-Effective Solutions:
Optimizing Mold Design: Reducing material waste and improving yield.
Recycling: Reusing excess metal and scrap from the casting process.
2. Forging
Advantages:
Strength: Produces pistons with superior mechanical properties.
Durability: Forged pistons typically have a longer lifespan.
Process:
Closed-Die Forging: Metal billets are heated and pressed into die molds under high pressure.
Precision Forging: Reduces the amount of machining required, saving material and time.
Cost-Effective Solutions:
Energy Efficiency: Utilizing modern, energy-efficient heating and pressing equipment.
Material Utilization: Minimizing material waste through precise billet sizing and efficient die design.
3. Powder Metallurgy
Advantages:
Material Efficiency: Produces minimal waste and allows for the use of composite materials.
Complex Shapes: Can create complex geometries that are difficult with other methods.
Process:
Powder Compaction: Metal powders are pressed into the desired shape.
Sintering: The compacted shape is heated to bond the powder particles.
Cost-Effective Solutions:
Bulk Production: Effective for high-volume production runs.
Recycling: Utilizing leftover powder and scrap material.
4. Additive Manufacturing (3D Printing)
Advantages:
Design Flexibility: Can produce highly complex and customized designs without additional tooling.
Low Waste: Additive process results in minimal material waste.
Process:
Selective Laser Melting (SLM): Metal powder is melted layer by layer using a laser.
Direct Metal Laser Sintering (DMLS): Similar to SLM but typically used for different types of metal powders.
Cost-Effective Solutions:
Prototyping: Ideal for low-volume production and prototyping.
Design Optimization: Reducing material usage through topology optimization.
5. Properties and Characteristics
▶Pistons are critical components in engines and various mechanical systems, and their performance is determined by several key properties and characteristics. These include material properties, mechanical strength, thermal behavior, and design features. Below are the detailed properties and characteristics of pistons:
1. Material Properties
Common Materials:
Aluminium Alloys: Known for their lightweight, good thermal conductivity, and adequate strength.
Cast Iron: Offers excellent wear resistance and durability.
Steel: Provides high strength and resistance to thermal fatigue.
Composites: Advanced materials designed for specific high-performance applications.
Material Characteristics:
Density: Influences the overall weight of the piston and engine efficiency.
Thermal Conductivity: Affects the ability to dissipate heat generated during operation.
Coefficient of Thermal Expansion: Impacts the dimensional stability under varying temperatures.
2. Mechanical Strength
a) Tensile Strength:The ability of the piston material to withstand pulling forces without failing.
b) Compressive Strength: The ability to withstand compressive forces encountered during the combustion cycle.
c) Fatigue Strength: The ability to resist failure under cyclic loading, which is critical due to the repetitive nature of piston motion.
d) Hardness: Resistance to surface wear and abrasion, which affects the longevity of the piston.
3. Thermal Properties
a) Heat Resistance: Ability to operate at high temperatures without degrading. Pistons must handle the heat generated by combustion efficiently.
b) Thermal Expansion: Pistons expand when heated. Managing this expansion is crucial to maintain proper clearances and avoid seizing or excessive wear.
c) Thermal Conductivity: Efficient heat dissipation is vital to prevent hotspots and ensure uniform temperature distribution.
4. Design Features
Shape and Geometry:
a) Crown Design: The top surface can be flat, domed, or have a complex shape to optimize combustion.
b) Skirt Design: Helps in guiding the piston in the cylinder and reducing friction.
c) Piston Rings: Typically include compression rings and oil control rings, which seal the combustion chamber and control oil consumption.
d) Weight: Affects the reciprocating mass and, consequently, the engine’s balance and performance.
e) Clearance: The gap between the piston and the cylinder wall, which is critical for thermal expansion and lubrication.
5. Wear and Friction Characteristics
a) Surface Finish: A smooth surface finish reduces friction and wear between the piston and cylinder wall.
b) Lubrication: Proper lubrication minimizes wear and heat buildup, enhancing the piston’s lifespan.
c) Coatings: Advanced coatings like molybdenum or ceramic can be applied to reduce friction and improve wear resistance.
6. Durability and Longevity
a) Fatigue Life: Pistons must endure millions of cycles without failure. High fatigue resistance is crucial for reliability.
b) Corrosion Resistance: Resistance to corrosion from fuel and combustion by-products is essential for long-term durability.
c) Wear Resistance: The ability to resist abrasion and wear from contact with the cylinder wall and piston rings.